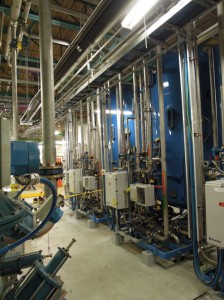
A row of mixed-bed demineralizers. A proper regeneration of demineralizer will increase cycle life and efficiency.
One of the key (and most expensive) parts of a high-quality water treatment plant is the mixed-bed demineralizer. Here are a few tips and tricks to consider during the regeneration cycle:
(Note: the process may differ for your units. Apply these tips with due diligence. I didn’t write this article as a complete overview of a mixed-bed demineralizer. This article is for trained water treatment plant operators.)
Extend the backwash
The backwash of a mixed-bed demineralizer will separate the cation and anion resin beads. A good separation is crucial to ensuring that the right beads get soaked in either caustic or acid. A really good separation should look like this. Notice the anion beads are on the top and the cation beads are on the bottom. A good backwash of 30 minutes achieved these results and by watching the sight glass closely for the formation of the “dividing line”. Also, make sure the resin bed does not climb too high in the vessel as to flow out of the backwash outlet (that would be thousands of dollars of resin going down the drain).
Drain down the waste tank (if you have one)
Right after the backwash is done, pause the regeneration and neutralize and drain the waste tank. No damage to the resin beads will occur and it will save you from dealing with a high waste-tank level later on in the regeneration. This tip is especially useful if you are doing a “doube-regeneration” (essentially all chemical injection times are doubled) on a really exhausted unit.
Extend the preheat wash down
The preheat step of a mixed-bed demineralizer regeneration is to prepare the anion beads for the dilute caustic injection step. Soaking the anion beads in hot water will flush the impurities captured from water entering the unit during service. The hot water will also warm up the caustic supply pipes, making it easier for the caustic to flow during the regeneration. For these two reasons, it is best to extend the preheat step for a bit longer. The amount of time really depends on experimentation and what your operating procedures call for.
This tip really depends on the size of your hot water tank. Some water treatment plants can only supply so much hot water for a process before running out. Also, the preheat step is a great time to ensure all your dilution water flows are within operating range and key valves are working.
Watch everything like a hawk during the chemical injection
A good operator will keep a close eye on everything during the chemical injection steps during a regeneration. Some process systems regenerate each of the resins individually or both at the same time. If dilution water flows were not checked during the preheat step, and they are off, things will get ugly really fast. Keep an eye on chemical concentrations and address any issues promptly.
Extend the final chemical displacement step
This is really a personal choice but may help with conductivity issues later on during the rinse-down steps. If there is hot water to be spared, keep this step running for as long as you can to really remove any chemical residuals that are left over from regenerating the resin beads.
Just after the air mix, neutralize the waste tank
Just after the air mix, pause the regeneration process and neutralize and empty the waste tank. This will prevent headaches from the final rinse step.
And there you have it
I hope that these tricks and tips will be of use. Above all, the most important piece of advice is to know your system inside and out. Good luck with your future regenerations on your mixed-bed demineralizers.